Cart
This product is not clubbable with other items in cart. Please remove this or other items to proceed further.
This product is not clubbable with other items in cart. Please remove this or other items to proceed further.
Deleting
Products from multiple soldto's are in cart. Only products from single soldto is allowed in cart.
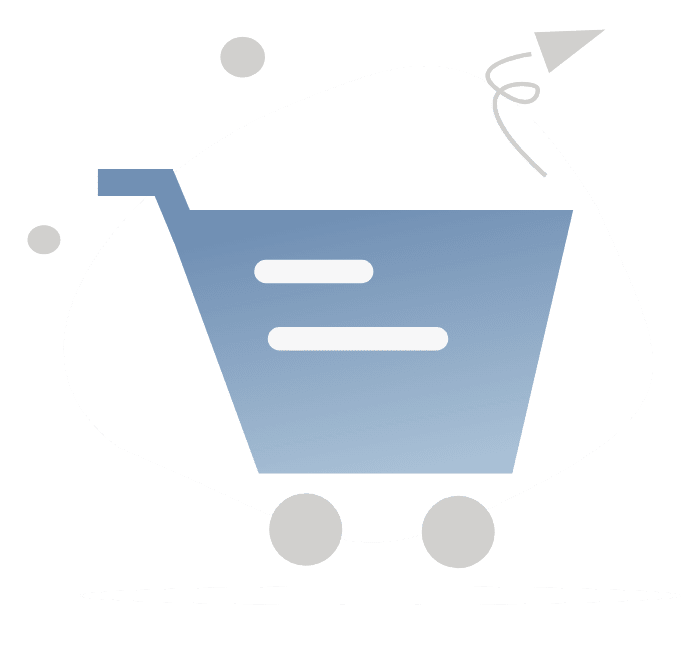
No Items In Cart