De-Risk the Transition to Prefilled Syringes with Performance Testing
Traditionally, drugs and biologics have been sold in vials. Utilizing a vial system requires the use of a syringe or other transfer device to withdraw the medication from the vial and facilitate delivery directly to the patient or to an IV bag for subsequent administration to the patient. These steps can result in errors, spills, contamination, or other mishaps. A simplified approach for administration has been to package the drug or biologic as a pre-filled syringe combination product. Drug administration is then made easier because the syringe is both the containment system and the delivery system such that the drug can be directly injected into a patient or into an IV bag port.
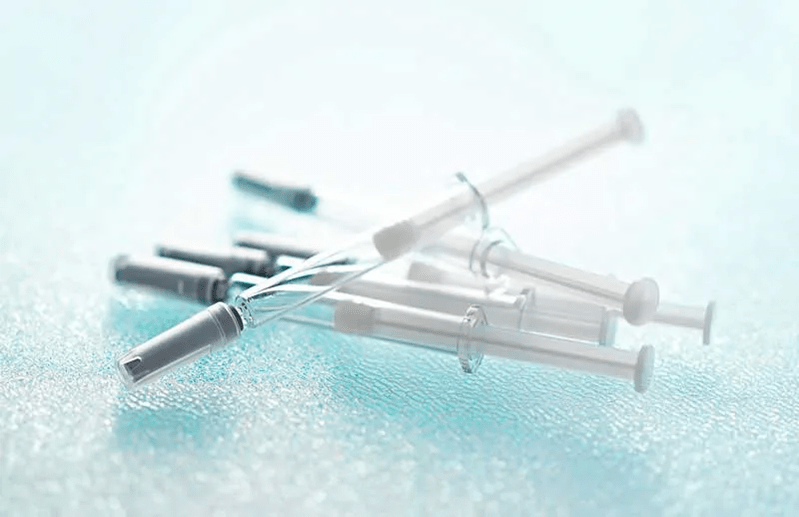
There are standards and normative references published by the International Organization for Standardization (ISO) which address the recommended testing for single use syringes, ISO 7886-1,i glass pre-filled syringe barrels, ISO 11040-4,ii plastic pre-filled syringe barrels, ISO 11040-6,iii and finished pre-filled syringes, ISO 11040-8.iv In addition to the performance tests recommended in those standards, one should consider how the pre-filled syringes would be shipped, stored and used. As a result, shipping simulations per ASTM D4169-22,v plunger movement studies per ASTM D6653-13,vi cool/standard/warm storage per ISO 11608-1:2022,vii and other conditioning may need to be considered, based on risk assessments, as described in ISO 14971,viii around the product’s life-cycle, including intended distribution, intended storage and intended use conditions of the combination product. Overall, it is important to consider ISO Standards only as starting points and not as a complete and limiting list of required tests. The final set of tests carried out to demonstrate performance of the combination product should always be based on risk assessments pertinent to the specific combination product being considered.
Pre-filled syringe performance testing, according to ISO 11040-8, includes evaluation of the following:
- Critical dimensions, including interfaces to sharp injury prevention devices, connectivity to fluid path connectors (e.g., needles, ports and vial adaptors), plunger position, plunger and barrel dimensions and fit, etc.
- Break loose and extrusion forces, throughout the shelf life of the device, to ensure the user can successfully deliver the intended dose
- Burst resistance to ensure that when flow through the intended point of syringe egress (needle, catheter, port, etc.) is restricted, the user does not over-pressurize the syringe with excessive plunger rod pressure and cause leakage through the Luer connection or between the plunger and barrel
- Break resistance for the finger flange and for the Luer cone to ensure the user would not easily break the device while holding the device or while connecting to the Luer end
- Closure system forces and torques, including unintended actions like Luer lock adaptor collar pull-off force and twist-off torque and intended actions like Luer lock rigid tip cap unscrewing torque and tip cap or needle shield pull-off force
- Residual volume and deliverable volume to ensure the correct dose is administered
- Needle penetration force to ensure skin can be punctured with minimal pain and discomfort by staked needles
- Needle pull-out force to ensure syringes with staked needles cannot leave their needle behind in the patient or in the needle injection port on an IV bag
- Liquid leakage beyond the plunger to ensure that if the plunger rod is angled to the side of the barrel during administration, the distortion does not open up a leak path between the plunger and barrel
- Accuracy of graduation marking to ensure doses can be accurately measured and dispensed when the complete contents of the syringe is not the intended dose
- Extractables,ix leachables,x drug and syringe material-of-construction compatibility and the effect of shear forces on the quality of the drug to ensure the drug is not degraded or contaminated by packaging as a combination product
- Sterility, endotoxins and Container Closure Integrityxi (CCI) to ensure there is no biological contamination of the drug product
- Particulate content to ensure the drug is not contaminated with excessive particlesxii
Many of the above tests apply to the combination of components used in the prefilled syringe regardless of the drug. The results of these tests may be available from the syringe supplier and may not require testing by the manufacturer of the combination product. However, if generation of test results is required, much of this testing is available with West. Testing that is unique to the combination product, comprising the device and the drug or biologic, includes break loose and extrusion, burst resistance and liquid leakage, leachables, compatibility, shear forces, sterility, endotoxins, CCI and particles and must be performed on the finished product. In addition, tip cap or needle shield removal force is often considered an Essential Performance Requirement for pre-filled syringes and should be considered for release testing.
Break loose and extrusion is a physical variable test method. While ICH guidelinesxiii describe the approach for validating chemical test methods, including specific validation characteristics that must be considered, this approach is not very meaningful for physical test methods. Variable physical test methods are validated against the following characteristics:xiv
- Accuracy – demonstrated through calibration of the measuring instrument(s)
- Stability – demonstrated through periodic recalibration and a daily calibration check of the instrument(s) to show the absence of drift in the measurements
- Precision – demonstrated through a Gage Repeatability and Reproducibility study (Gage R&R) where the repeatability of a measurement (repeat measurement of the same part by the same operator) and the reproducibility of a measurement (reproduction of a measurement by a different operator, or by multiple different operators) are evaluated and documented
For destructive test methods, such as break loose and extrusion, where the execution of the test alters the device being tested (e.g., the lubricant on the plunger is spread across the barrel during use such that a reuse would produce a different force measurement), a Gage R&R can be a challenging endeavor. Often, one might assume a single lot of pre-filled syringes should have the same performance and therefore assess repeatability by testing two different syringes as if they were the same syringe tested twice. However, this often produces results that erroneously suggest poor precision because the calculation of precision incorrectly assigns part-to-part variation to poor repeatability-and-reproducibility.
Since the goal of a Test Method Validation (TMV) is to demonstrate the test procedure and equipment produce reliable results, one does not need to test actual devices for the purpose of method validation but one can, instead, test surrogate devices which are not destroyed in the testing process and can thus be used to assess repeatability-and-reproducibility. West has developed and validated platform methods for testing devices based on specially designed surrogates. In the case of break loose and extrusion, the surrogate is comprised of a spring-loaded device that can repeatably and reproducibly yield a consistent force upon compression. West can meet clients’ Test Method Validation needs by simply performing a Test Method Verification on the client’s device against the existing platform validation. This approach allows for faster turn-around for the client, requires fewer devices and produces ready and validated methods at a lower cost.
West analytical lab services group has validated platform methods for pre-filled syringe testing at our Exton, PA, USA laboratory and at our Waterford, Ireland laboratory. West’s analytical services laboratory in Exton is US-FDA inspected and the Waterford laboratory is an Irish-HPRAxv accredited facility located in an EU Member State ready to perform stability and release testingxvi for combination products. To learn more about our testing capabilities click here. For additional questions contact us today.
References
i. ISO 7886-1:2017 Sterile hypodermic syringes for single use – Part 1: Syringes for manual use
ii. ISO 11040-4:2015 Prefilled syringes – Part 4: Glass Barrels for injectables and sterilized subassembled syringes ready for filling
iii. ISO 11040-6:2019 Prefilled syringes – Part 6: Plastic Barrels for injectables and sterilized subassembled syringes ready for filling
iv. ISO 11040-8:2015 Prefilled syringes – Part 8: Requirements and test methods for finished prefilled syringes
v. ASTM D4169-22 Standard Practice for Performance Testing of Shipping Containers and Systems
vi. ASTM D6653-13 Standard Test Methods for Determining the Effects of High Altitude on Packaging Systems by Vacuum Method
vii. ISO 11608-1:2022 Needle-based injection systems for medical use – Requirements and test methods – Part 1: Needle-based injection systems
viii. ISO 14971:2019 Medical devices – Application of risk management to medical devices
ix. USP. Assessment of Extractables Associated with Pharmaceutical Packaging/Delivery Systems <1663>. In: USP–NF. Rockville, MD: United States Pharmacopeia.
x.USP. Assessment of Drug Product Leachables Associated with Pharmaceutical Packaging/Delivery Systems <1664>. In: USP–NF. Rockville, MD: United States Pharmacopeia.
xi. USP. Package Integrity Evaluation—Sterile Products <1207>. In: USP–NF. Rockville, MD: United States Pharmacopeia.
xii. USP. Particulate Matter in Injections <788>. In: USP–NF. Rockville, MD: United States Pharmacopeia.
USP. Visible Particulates in Injections <790>. In: USP–NF. Rockville, MD: United States Pharmacopeia.
xii. ICH, 2005. Q2 (R1), “Validation of analytical procedures: text and methodology”, ICH Harmonised Tripartite Guideline. International Conference on Harmonisation of Technical Requirements for Registration of Pharmaceuticals for Human Use, Chicago, USA, 2005.
xiv. Taylor, Wayne (2017) Statistical Procedures for the Medical Device Industry. Taylor Enterprises, Inc.
xv. The Health Products Regulatory Authority (HPRA) is the Irish regulatory agency for medicines, medical devices and other health products.
xvi.Directive 2001/83/EC of the European Parliament and of the Council of 6 November 2001 on the Community Code Relating to Medicinal Products for Human Use, which states that medicines that are manufactured outside the EU, in countries that do not have a Mutual Recognition Agreement with the EU, must be retested within an EU Member State for release.
West Services and Solutions, LLC, a subsidiary of West, handles many of the tests described above.