Ensuring Sterility with West’s Ready-to-Use Offerings
Ensuring the sterility of sterile medicinal products has always been one of the key concerns of drug manufacturers, due to the dire health implications it could have on the patients, as well as the potential for costly product recalls. The importance of control strategies to ensure sterile drug products has also been reiterated by regulatory agencies such as the U.S. Food and Drug Administration (FDA) and The European Medicines Agency (EMA) in their respective guidelines:
- FDA – Sterile Drug Products Produced by Aseptic Processing – Current Good Manufacturing Practice
- EU GMP Annex 1 Manufacture of Sterile Medicinal Products
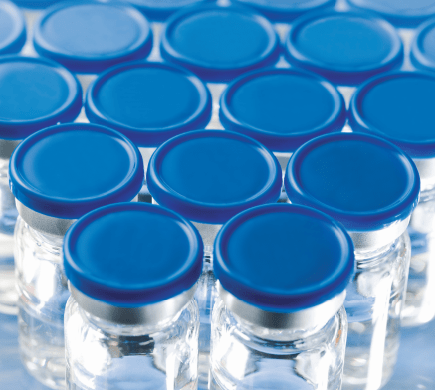
In both guidances, sterile products entail minimal risks of particulate, endotoxin, and microbial contamination. Particulate and microbial contamination are minimized with the implementation of high-quality environmental conditions for different stages of the manufacturing process. This could be achieved with the use of clean rooms of the appropriate class (ISO class 5 to 8) or even restricted access barrier systems (RABS) and isolator systems in the case of aseptic processing. However, additional control measures are still needed for further reduction of endotoxin and microbial contamination. This involves adequate depyrogenation and sterilization processes.
For containers and closures, one common depyrogenation technique involves the use of Purified Water, USP or Water for Injection (WFI) to rinse the containers or closures over multiple cycles prior to sterilization. Regardless of the technique utilized, the depyrogenation process should be validated to meet a 3-log reduction in endotoxin content.
Sterilization of Elastomers
To ensure sterility, a sterility assurance level (SAL) of 10-6 or better is attained to qualify the sterilization cycle. Validation studies are carried out to ascertain the effectiveness of the sterilization process, followed by periodic requalification studies. Depending on the stability of the parenteral packaging material and drug product, different sterilization techniques could be used. This includes moist heat, dry heat, radiation, ethylene oxide and filtration techniques.
It could not be overstressed how important sterile components are to drug manufacturers. To meet the increasing demands from pharmaceutical and biopharmaceutical companies, West has thus introduced various ready-to-sterilize (RS) and ready-to-use (RU) products to aid our customers in getting their drugs to the market in the shortest possible time.
Parenteral Packaging Components
One example is the Westar® RS/Westar® SELECT RS elastomeric components that are delivered to customers as ready-to-sterilize components together with a Quality Certificate. Such products have undergone a validated pharmaceutical wash process that allows them to meet the specified limits for bacterial endotoxin, bioburden, particulate matter and where applicable, silicone level. Importantly, a 3-log reduction in the endotoxin content is also ascertained during the validation study for the pharmaceutical wash.
Westar® RU/ Westar® SELECT RU elastomeric components further simplify the processes on the customer end as these components are delivered as ready-to-use and have already been sterilized by steam sterilization or gamma irradiation (validated to achieve SAL of 10-6 or better) after undergoing the validated pharmaceutical wash process. A Quality Certificate will be provided with the following product specifications – sterility assurance (only for steam sterilization; for gamma irradiated components, gamma dose range is reported), particulate matter content, bacterial endotoxin levels, silicone level (when applicable) and residual moisture (lyophilization stoppers only).
EMA Annex 1- Vial Capping
In recent years, the EMA Annex 1 “Manufacture of Sterile Medicinal Products” has included the vial capping conditions required for both aseptic and clean processing. While sterilized caps / seals must be used in an aseptic process, the seal grade was not stipulated for the clean process, as long as crimping is performed in a grade A environment. West has thus developed Flip-Off® CCS and Flip-Off® Plus seals that could meet such stringent regulatory requirements, with sterilization fulfilled by gamma irradiation.
West’s Flip-Off® CCS (Clean, Certified, Sterilized) seal, as suggested by its name, is a high-quality sterile seal that is provided primarily in an RU grade (Flip-Off® CCRS seal grade also available). These sterilized seals are developed for aseptic crimping in a grade A environment. Some key features include an aluminum shell coating that reduces abrasion, hence keeping particle level low. The seals are also assembled in an ISO 8 environment, thereby allowing low particle level and low bioburden level before sterilization.
West’s Flip-Off® Plus seals, on the other hand, are developed for clean crimping in a grade A environment. Provided in both RU and RS grades, these seals make use of West high-quality aluminum and polymer materials that are assembled in a controlled environment, to ensure a controlled bioburden level before sterilization.
While glass is commonly used in the drug containment system such as vials or prefilled syringes, they may be incompatible with high and low pH drug products that could result in glass delamination as well as a compromised container closure integrity under cryogenic storage. Thus, West offers the solution of using Daikyo Crystal Zenith® (CZ) cyclic olefin polymer containment solutions for such drug products. CZ containment solutions are provided as bulk non-ready-to-use format, and ready-to-use format, which is sterilized by a validated e-beam sterilization process (SAL of 10-6 or better).
Packaging for parenteral packaging components
As West understands the importance of packaging for these parenteral packaging components to allow proper sterilization and usage, especially in aseptic processing, the validated STERILIZABLEBAGTM packaging system is used to contain RS and RU components. This packaging system consists of the Tyvek® 1073B packaging material and a multi-layered polyethylene film. While the Tyvek® 1073B [1] packaging material allows steam permeation, it also acts as a barrier to prevent bacterial ingress, thereby helping to ensure sterility. The multi-layered polyethylene film on the other hand helps to maintain the package integrity after sterilization, shipping and throughout the product shelf-life.
With the introduction of restricted sterile systems such as isolator / RAB systems in aseptic processing, it is important to ensure that the parenteral packaging components could be aseptically transferred to the filling line. To meet such a requirement, West also offers the choice of RS or RU components filled in port bags. These port bags are Biosafe® bags and DPTE® BetaBags from Sartorius Stedim Biotech and GETINGE, respectively, which could undergo steam sterilization or gamma-irradiation. Such bags contain a beta port that could connect to the alpha port of restricted sterile systems that will facilitate the aseptic transfer of the parenteral packaging components.
While the above examples do not represent an exhaustive list of RS and RU product offerings available, it demonstrates West’s commitment in providing the highest quality parenteral packaging components that could support the pharmaceutical manufacturers in assuring drug product sterility. For more information on West products and how the different sterilization techniques could be employed to packaging components to meet the regulatory challenges, contact a Technical Customer Service (TCS) representative or account manager or visit our Knowledge Center.
References
[1]"Tyvek® 1073B," Dupont, [Online]. Available: https://www.dupont.com/products/tyvek-1073b-medical-device-packaging.html. [Accessed 19 November 2021].
Westar, Flip-Off, and STERI
LIZABLEBAG
TM are trademarks or registered trademarks of West Pharmaceutical Services, Inc. in the United States and other jurisdictions.Crystal Zenith is a trademark of Daikyo Seiko, Ltd. Crystal Zenith technology is licensed from Daikyo Seiko Ltd.All other trademarks appearing here are the property of their respective trademark owners.