Control Strategy: What, When, Where and Why for Drug-Device Combination Products
There are clear gaps in understanding in the market of combination products. A major one was highlighted at a recent workshop sponsored by West. A survey showed that over 20% of attendees were not aware of the considerations needed to build a control strategy.
![]()
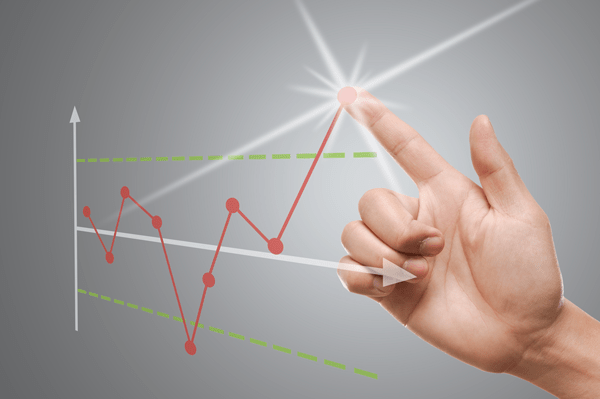
A control strategy is defined as a planned set of controls, derived from product and process understanding, that assures process, performance, and product quality.1 Building a control strategy starts with understanding the product and process; this understanding must begin in development. More specifically, building a control strategy comprises understanding the connectivity among materials of composition, components, constituent parts, final drug-device combination product, and critical process parameters.
An aid to building a control strategy is ICH Q12 (Technical and Regulatory Considerations for Pharmaceutical Product Lifecycle Management)2 which presents the key concept of established conditions. Established conditions are the elements of the control strategy that are necessary to assure product quality. Note that if established conditions are changed post-approval, an update of the regulatory submission is needed.3 The major regulatory agencies, including the FDA, support the use of ICH Q12. However, local regions/agencies may have a unique perspective in use, since this guidance is relatively new. Another key concept is essential performance requirements (EPRs). EPRs are considered by the Center for Devices and Radiological Health (CDRH) to be a subset of design controls that relate to assuring that clinical performance of the device itself is adequate to meet the combination product performance intended at the point of dosing.3
Building a control strategy requires risk-based consideration of routine controls that is focused not only on the essential functions of the combination product, but the aspects of the components that contribute to the essential functions. There should be a process map, developed and documented, to understand what may influence the critical quality attributes (CQAs) of the combination product. With this process map, control points based on the impact to the CQAs can be established. At this point there should be a clear understanding from an internal knowledge management standpoint, which will provide the supportive data that may be requested by a regulatory agency.
Focus should always be on safe and effective use, that is, proper functioning of the drug product, the device, and the combination product. Considerations should be given from the materials perspective, the components perspective, and the total system perspective, in particular how each perspective is influenced by processing.
Controls to be considered throughout the process are:4
- Purchasing/supplier controls
- External manufacturing controls
- Incoming controls
- Manufacturing control plans
- Packaging and labeling controls
- Final testing and release
It always makes sense to push these controls as far upstream as possible to minimize the risk of identification of quality issues downstream when there are more costs and time built into the product. Tests should be placed nearest to the closest potential point of failure.
In the example below, an EPR of an autoinjector system has been defined as maximum activation force. Traditionally, an approach from a control standpoint would be to test the product at the end of production. With the more up-to-date approach, controls would be pushed upstream to different key points in the process. See Table 1. These would be mapped to show the connectivity to the quality of the combination product. Of course, as noted, the relationship among these points and their impact to the final combination product must be understood.
Table 15

A holistic approach to control strategy can be thought of more broadly than just a product control strategy. Organizations are expected to provide holistic oversight of product quality and performance by maximizing the advantages of connectivity, digitization, monitoring, control and real-time data-driven decisions.6 An approach such as this can be executed correctly only if there is a good understanding of critical quality attributes and critical process parameters throughout the supply chain. To do this, relationships with suppliers and partners must be established. This is one of the main reasons why interactions with both upstream and downstream product and service suppliers are so important to combination product development and manufacturing.