Design and Building of Fixtures and Surrogates for Combination Product Performance Testing
The combination product market has seen steady growth,i driven primarily by the rise in chronic disease indications, the demands for self-administered therapies and technological advancements in drug-delivery devices. Drug- or biologic-led combination products are typically a pharmaceutical product pre-packaged in a device that can be used for administration. The use of combination products simplifies the process of drug administration for the patient and/or the caregiver and, in some cases, allows the patient to receive treatment at home rather than having to travel to a medical facility, thus easing the burden on patients and helping facilitate drug regimen adherence. However, there are many challenges that need to be navigated as one considers the transition from a vial system to a needle-based combination product.
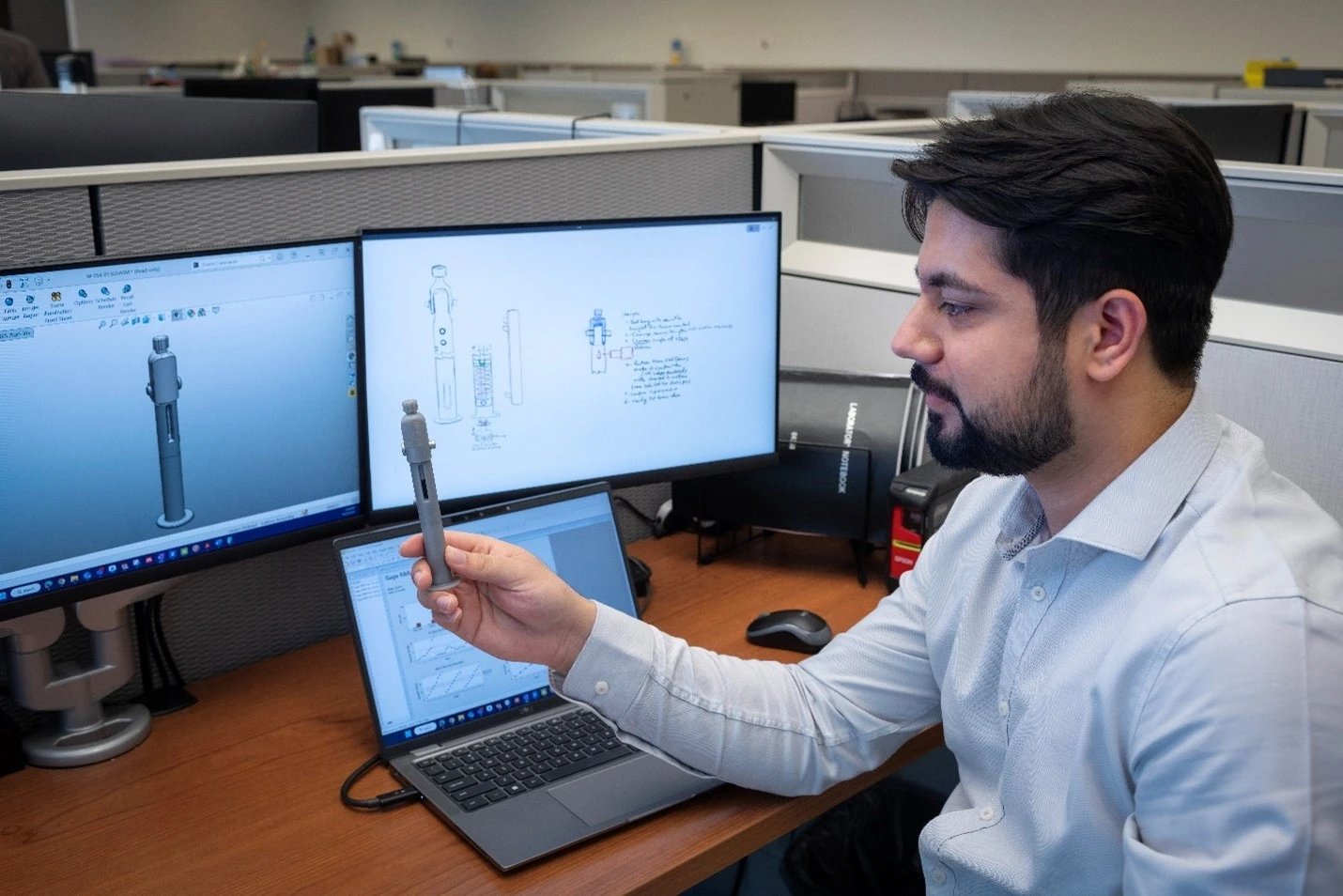
The device constituent of a combination product must be developed according to Design Controls, as described in 21 CFR 820.30ii and in ISO 14385iii. The development process involves setting Design Inputs (or what the product needs to do), generating Design Outputs (or what the product actually does), and then demonstrating that the Design Outputs meet the Design Inputs through laboratory-based Design Verification Testing. This testing is often based on international standards, such as the ISO 11040 series for syringes and the ISO 11608 series for needle-based injection systems, as well as risk assessments of the combination product that evaluates both anticipated and unanticipated failure modes. West has previously described some of the standard laboratory test methods that are routinely performed in West’s analytical services laboratory for pre-filled syringes and autoinjectors.
While international standards cover an extensive range of combination products, there may be unique designs that require special considerations for performance testing and so the product developer may need to perform custom testing. Even for tests described in international standards, not all fixtures necessary to hold, manipulate and test combination products may be commercially available. In many cases, custom fixtures and test setups need to be designed and built to perform testing of combination products.
Once test methods are developed, either based on international standards or specifically for unique devices, test method validation must be performed to establish the precision of the test method. This validation involves performing a Gage Repeatability and Reproducibility (Gage R&R) study where each operator tests the same device multiple times to establish repeatability, and then different operators test the same device to establish reproducibility. This type of precision assessment works well for non-destructive test methods but destructive test methods, such as breakloose and extrusion on a prefilled syringe, are more challenging to evaluate. Once the plunger in a pre-filled syringe is broken loose from its position and the contents of that syringe have been extruded, refilling that syringe will not result in a pre-filled syringe with the same breakloose or extrusion forces because the syringe lubrication was altered and the exact conditions of the plunger and barrel have been modified. The best way to evaluate precision on destructive test methods is to design and build a surrogate device that looks and operates like a real device, fits into the same test fixture as the original device but can be repeatedly tested non-destructively. This approach allows for a proper Gage R&R study to assess the true precision of the test method being validated.
To design and build fixtures and surrogates for Design Verification Testing, a contract laboratory needs experienced mechanical and biomedical engineers on staff that can work with clients to design custom solutions for their unique needs. In addition, 3D printing capabilities and a means to build custom machined parts are vital to quickly design, prototype and build fixtures and surrogates.
West’s analytical laboratory has several mechanical and biomedical engineers available to design custom test equipment for our clients’ unique combination products. The laboratory utilizes agile methodology and iterative models to create unique designs for addressing complex device testing problems and leverages in-house fused deposition modeling (FDM) and stereolithography (SLA) 3D printers to prototype or create parts of limited manufacturability. Parts that require higher strength and/or surface finish are built in aluminum or steel through our contract manufacturers (CMs) to meet our design specifications. These capabilities allow West’s analytical laboratory to quickly design, build and test solutions for unique combination products testing.
For example, in order to validate platform test methods for typical pre-filled syringe tests, as described in ISO 11040-8iv and ISO 11040-4v, West designed surrogates for methods such as Breakloose and Extrusion Forces, Needle Pull-Out Force, Flange Breakage Resistance Force, Luer Cone Breakage Resistance Force, Needle Shield or Tip Cap Removal Force and Luer Lock Collar Adapter Pull Off Force. These test methods were all validated as platform methods to demonstrate the ability of the force testing machine and the associated test fixtures to meet precision requirements through a Gage R&R study. Thus, when the time comes for West to perform Design Verification testing of a client's pre-filled syringe based combined product, only a method verification against the validated platform to demonstrate the device's compatibility with the platform method is required, thus significantly improving the turnaround time.
The West analytical lab services group has validated platform methods for pre-filled syringe testing at our Exton, PA, USA laboratory and at our Waterford, Ireland laboratory. West’s analytical services laboratory in Exton is US-FDA inspected, and the Waterford laboratory is an Irish-HPRAvi accredited facility located in an EU Member State ready to perform stability and release testingvii for combination products. To learn more about our testing capabilities click here. For additional questions contact us today.
[i] FY2022 Office of Combination Products Performance Report to Congress as required by the Medical Device User Fee and Modernization Act of 2002. Available at:
https://www.fda.gov/media/174973/download. Accessed August 2024.
[ii] 21 CFR 820.30.
https://www.ecfr.gov/current/title-21/chapter-I/subchapter-H/part-820.30. Accessed August 2024.
[iii] International Organization for Standardization. (2016)
Medical devices — Quality management systems — Requirements for regulatory purposes. (ISO Standard No. 13485:2016).
https://www.iso.org/standard/59752.html[iv] ISO 11040-8:2015 Prefilled syringes – Part 8: Requirements and test methods for finished prefilled syringes
[v] ISO 11040-4:2024 Prefilled syringes – Part 4: Glass Barrels for injectables and sterilized subassembled syringes ready for filling
[vi] The Health Products Regulatory Authority (HPRA) is the Irish regulatory agency for medicines, medical devices and other health products.
[vii] Directive 2001/83/EC of the European Parliament and of the Council of 6 November 2001 on the Community Code Relating to Medicinal Products for Human Use, which states that medicines that are manufactured outside the EU, in countries that do not have a Mutual Recognition Agreement with the EU, must be retested within an EU Member State for release.