Unveiling The Lens: Navigating Challenges in Envision Inspection Technology
In the realm of sterile pharmaceutical products, the pursuit of high-quality packaging components stands as the cornerstone of patient safety. The recent revision of the EU Good Manufacturing Practice (GMP) Annex 1, an integral guideline governing pharmaceutical manufacturing practices, has spotlighted the implementation of the Contamination Control Strategy.1 This strategic framework meticulously controls the management and mitigation of contamination risks. Amidst these risks lies particulate matter – a challenge that underscores the need for meticulous scrutiny within sterile pharmaceutical product manufacturing processes.
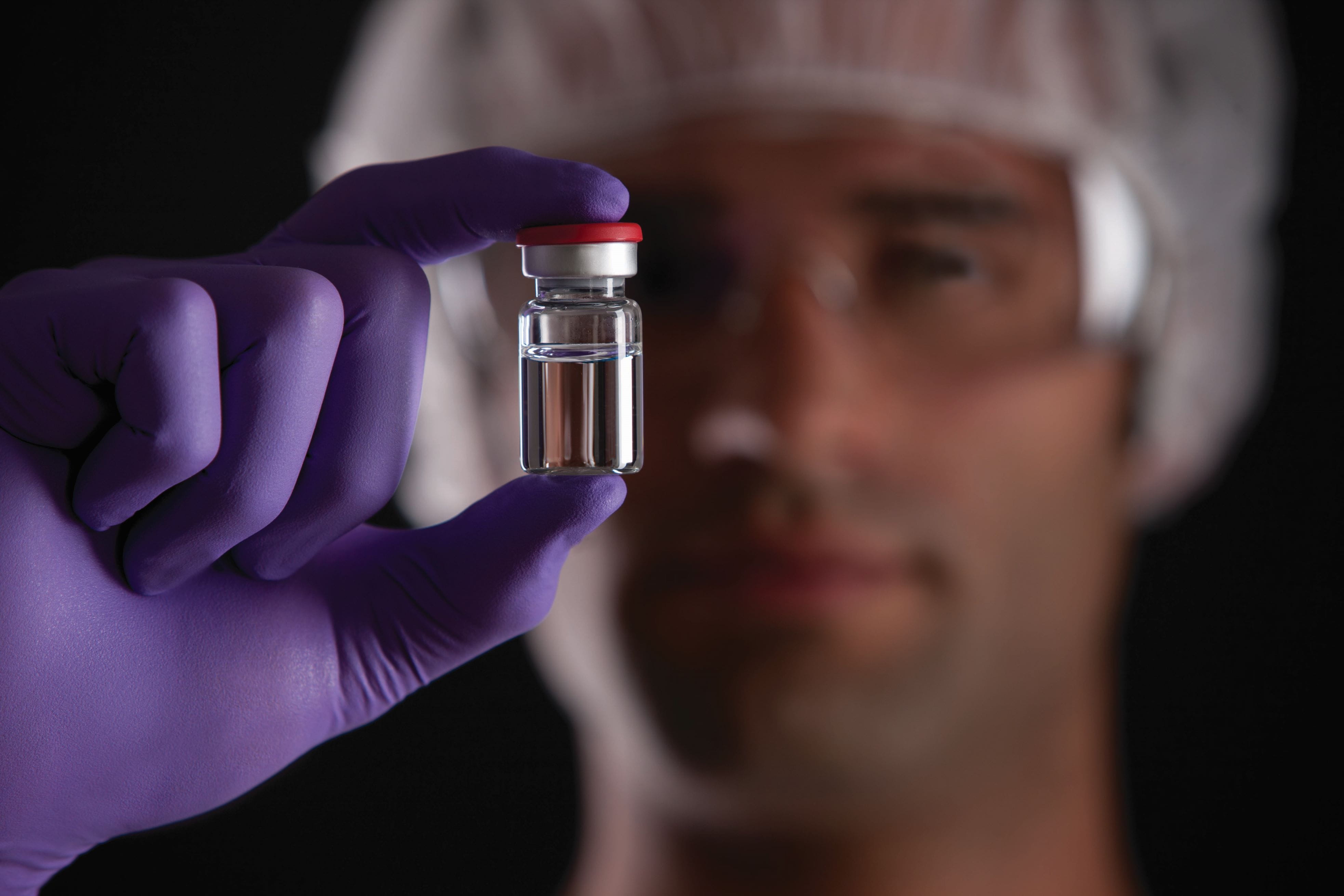
Automated inspection systems, such as West’s Envision™, is an automated 100% vision verification process, that can help to reduce component-related risks during pharmaceutical fill-finish operations by leveraging an automatic, program-controlled vision inspection technology to inspect surfaces of elastomeric components. This technology employs a sophisticated system that integrates high-resolution imaging, software, and algorithms to scrutinize pharmaceutical packaging components and is used to minimize risk of end of line rejects associated with elastomer quality attribute defects. This process takes place at the end of the manufacturing process after final washing in a Zone 5 cleanroom in an effort to ensure cleanliness, quality, and uphold customer satisfaction.
Types of Defects
Despite stringent manufacturing processes and quality control measures, there is still the potential for various types of defects to occur, posing challenges to product quality and performance. Understanding these defects is essential for pharmaceutical manufacturers. Some of the defects in pharmaceutical packaging components are:
- Particulates and fibers
This encompasses various instances of particulate and fiber contamination in pharmaceutical stoppers or plungers. It includes scenarios where particles or fibers are embedded within the stopper or plunger material, instances where they adhere to the surfaces, and situations where loose particles or fibers are present, potentially compromising patients’ safety if these contaminants interact with the drug or are injected into the patient. - Cosmetic issues
Cosmetic issues pertain to the visual appearance of stoppers or plungers. This includes concerns related to the surfaces, such as scratches or any imperfections that do not impact functionality but could affect the overall aesthetic appeal of the pharmaceutical packaging. - Intermix
Intermix refers to the presence of the wrong design in the pharmaceutical stoppers or plungers. This defect can occur when there is a mix-up or error in the intended design during the manufacturing process, potentially leading to issues in product performance or compatibility. - Forming defects
Forming defects encompass a range of issues related to the molding and trimming of stoppers or plungers. This includes deformities in the shape of the stopper or plunger, manufacturing marks that may affect functionality or aesthetics, and instances of damage to the stopper or plunger during the forming process.
How the Envision Verification Process works
The process begins after the Westar™ quality level wash process, whereby each component is passed through a series of cameras inspecting for defects. If the component exhibits a defect, such as the examples above, it is removed from the batch, delivering West’s required specification. This process helps reduce overall costs by minimizing the risk of drug product rejection due to visible particulates and closure defects.
The resulting West components can deliver reliable yields in drug fill-finish and maximize usage of vials and syringes, with the refined quality levels associated with Westar quality level specifications.
Principle of Envision Verification Process Technology: Bright vs Dark Field Illumination
One of the key elements of the Envision verification process inspection system is determining the type of lighting that is best suited for defect detection to achieve the optimal contrast – bright field lighting or dark field lighting. Both illumination techniques are crucial and are used depending on the types of defects to be detected.
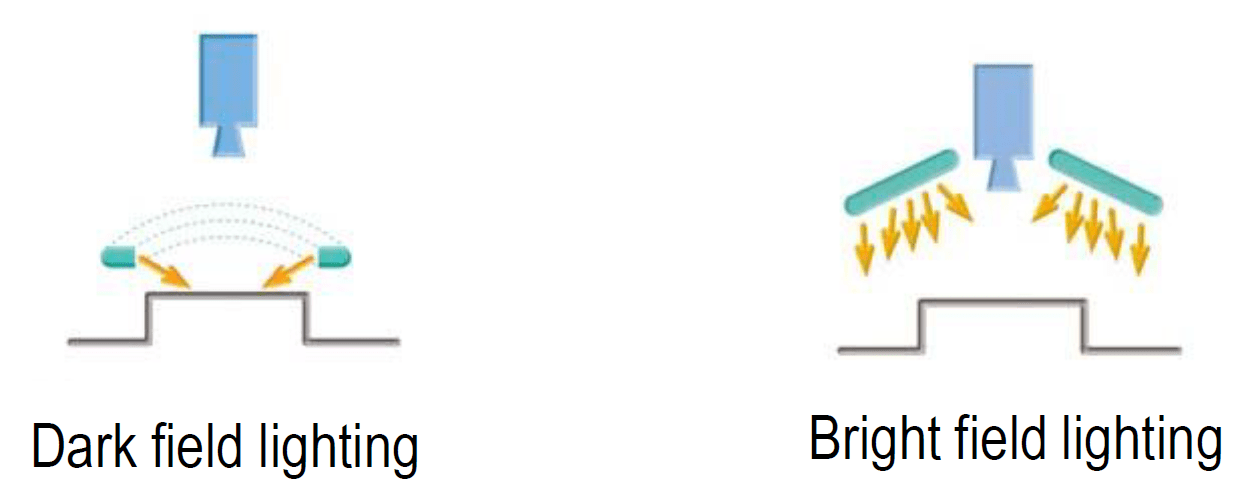
Figure 1. Lighting setup for a) dark field and b) bright field lighting
Bright field lighting is suita5ble for imaging reflected light, whereby the light from the source is reflected into the camera so that small defects and edges that typically scatter light are not captured by the camera. This creates a bright image, well-suited for detailed observation of specimens with varied color and surface characteristics, hence, making it ideal for detecting cosmetic or surface-level defects since any raised or indented features cast shadows that enhance their visibility. However, transparent fibers found on elastomeric components may result in poor visibility due to lack of sufficient inherent contrast. Regions with scratches or indentations may also not be as well defined for the same reason.
As opposed to bright field lighting, dark field lighting only captures scattered light. This type of lighting is ideal for detecting edges and surface defects as they can best scatter light. Optimally, a low angle of light is used to allow for edges, defects, and ridges to properly scatter the light while not having the surface of the component reflect too much light back to the camera. This technique can also be used to inspect highly reflective surfaces which would be a challenge with bright field lighting. An example is stoppers with film lamination that often have a glossy finish. Dark field illumination reduces glare and reflections on these surfaces, thus obtaining clearer images without the interference of excessive brightness.
Using both bright field and dark field lighting in tandem allows for a more thorough inspection. Bright field lighting highlights larger and more obvious defects, while dark field reveals finer details and surface irregularities. This combination improves the ability to detect and analyze a wide range of defects, ensuring higher quality and reliability of the inspection.Naturally, cameras and sensors are crucial in capturing high-quality images for analysis and detection of defects, but there are also other key components to the Envision verification process technology:
- Dynamic Lighting Control: Adjust illumination angles and intensity based on sample characteristics
- Image Processing Algorithms: Enhance and prepare images for analysis
- Feature Extraction Algorithms: Identify and extract relevant features from images
- Reference Standards: Predefined models or criteria for defect-free products
- Decision-Making Algorithms: Analyze extracted features and make decisions regarding acceptance or rejection
Challenges in Envision Verification Process Technology
At West, Envision verification process technology has revolutionized our quality control processes. However, despite its advancements, the system faces several challenges that impact its effectiveness in defect detection and analysis. Some of these challenges include:
- Low contrast
Certain areas on elastomeric components may have low contrast, making it challenging for the system to distinguish defects from the surface texture. For example, transparent fibers which are found on components can go undetected due to the absence of contrast, thus compromising the overall inspection accuracy. - Anti-sticking features
Anti-sticking features on elastomeric components can interfere with defect detection, creating false positives or obscuring actual defects, making it harder for the system to differentiate between intentional elements and real imperfections. - Size and location of defects
Small defects or those found in certain locations on the elastomeric components might be tough to detect consistently. This is due to the system’s inherent limitations in detection capability when these aspects fall below the system’s threshold for identification. For example, the interior area of lyophilization stopper comprise of complex geometries, such as curves, corners and recesses, which can be hard to access. These intricate structures can also create occluded areas or create shadows (due to insufficient lighting), making it difficult for the Envision verification process to capture detailed images for defect analysis. - Sensitivity and false positives
Increased sensitivity to detect smaller defects would increase the likelihood of false positives. It is therefore vital to find a balance between sensitivity for defect detection and minimizing false positives, which can be a challenge for the system. - Addressing these challenges involves continuous innovation, advancements in technology, and collaboration between industries and experts to enhance the capabilities of the visual inspection systems. Exploring the principles of visual inspection is a focal point aimed at gaining insights into effectively addressing challenges faced during the inspection process.
Conclusion
West is a leader in the design, development, manufacturing and processing of pharmaceutical packaging components, and meets stringent requirements for quality, assured through validated processes, and adheres to applicable cGMPs to satisfy customer’s requirements for high quality components. The Envision verification process, despite its challenges, represents a significant leap forward in ensuring the quality and safety of West’s pharmaceutical packaging components, and stands as a testament to the company's continuous pursuit of excellence. The Envision verification process plays a key role in the verification and reduction of defects and the enhancement of quality of products during pharmaceutical fill-finish operations. By incorporating advanced vision inspection technology, high-resolution imaging, and sophisticated algorithms, West demonstrates its commitment to advancing quality control measures. The Envision verification process not only addresses current challenges but also lays the foundation for continuous improvement of West's pharmaceutical packaging components, aligning with the company's reputation for innovation and excellence in the pharmaceutical industry.
For more information on West’s Envision verification process click here or contact an Account Manager or Technical Customer Support (TCS) representative.
References
1 2022, EU GMP Annex 1: Manufacture of Sterile Medicinal Products, https://www.gmp-compliance.org/guidelines/gmp-guideline/eu-gmp-annex-1-manufacture-of-sterile-medicinal-products [Accessed on 02 August 2023]