Overcoming the Challenges of Fill-Finish Manufacturing when Selecting Novel Containment Solutions
The need for advanced containment solutions, and novel fill-finish processing to enable implementation of these solutions, continues to grow as more complex drug products enter multiple pipelines. As biotech companies develop these complex drug products, the integration of product and process knowledge is crucial to delivering product safety, quality, identity, potency, and purity. And as biotech companies seek partners to help accelerate their development processes, West is committed to leading multi-disciplined, high-performance teams in developing optimal fill-finish solutions for novel packaging and container systems. This dynamic partnership is well-illustrated by the following case study.
![]()
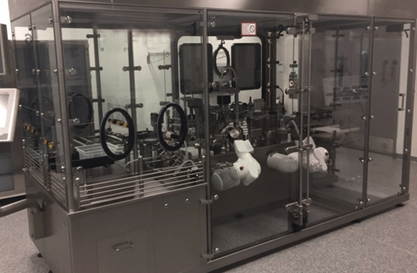
A biotechnology company introduced a novel monoclonal antibody for subcutaneous delivery, utilizing a container closure system that best suited the molecule needs. The delivery requirements of this monoclonal antibody necessitated dosing at various fill volumes to accommodate the needs of a diverse patient population, while still maintaining accurate dosing, stoppering, and container closure integrity (CCI) specifications for each dose iteration.
First, West provided a Daikyo Crystal Zenith® cartridge and a piston with a FluroTec® barrier film – to ensure optimal product stability over the intended shelf-life. With a phased approach to manufacturing scale up, this novel containment solution had to be implemented at both the company's manufacturing site, as well as at the contract manufacturing organization's (CMO) site.
Next, to demonstrate feasibility, the West Pharmaceutical Processing Group (PPG) developed and implemented various fill-finish processes utilizing an in-house custom flexible filler. By utilizing the in-house R&D flexible filler, the West PPG team, in collaboration with the customer’s engineering team, were able to evaluate different fill-finish parameters for dosing and piston placement that would impact the final performance of the container system. By conducting 100% IPC (in process controls which include fill volume/weight and piston position) on the fill-finish line, the optimal parameters were defined without having to break into a commercial line or take up capacity at the CMO, saving both time and resources during the early phase. A mimic solution with identical physical properties to the drug product was used to evaluate performance equivalency. Filled containers were then sent to West Analytical Lab Services for performance testing such as container closure integrity (CCI), freedom from leakage, and break-loose and glide force (BLG). Conforming results were the gate to implementing a technology transfer from the flexible filler to the company's filling line, and ultimately to the CMO.
Two years after the CMO technology transfer, an anomaly occurred involving the dosing and stoppering process. The company, CMO, and West collaborated to conduct a root cause investigation which identified 10 potential root causes. Components from the same lot used by the CMO were evaluated on the West flexible filler. This allowed for a quick investigation that did not tie up the line at the CMO. The anomaly was determined to be the increased line speed at the CMO, as they ramped up to larger-batch productions. Updated fill and machine parameters were then provided to the company and CMO to aid the CMO in refining the fill process for the increased throughput.
Collaborations and partnerships in the pharmaceutical and primary packaging businesses are key to the sustainability of long-term productivity, especially when developing a fill-finish manufacturing strategy. With the rise of more complex therapies and the increase in combination products, building and strengthening both existing and new partnerships is allowing West to better support customers as they navigate through the complexities of the fill-finish landscape. Successful collaborations and partnerships involve the participation of multiple parties including the fill-finish equipment manufacturer, the CMO, the pharmaceutical manufacturer, and West. Maintaining these collaborations and partnerships allows the stakeholders to monitor and stay ahead of trends and evolutions occurring in the pharmaceutical industry. West’s unique relationships with the key stakeholders and in-house technical expertise de-risk the pathway for product adoption and combination product development.
Many drug developers are challenged to find fill-finish solutions for the broad variety of drug product packaging and containment options available on the market. With a partner that is uniquely positioned to help Simplify the Journey™ from concept to commercialization, drug developers can de-risk their process with the flexibility, quality, speed, and expertise provided through West fill-finish and additional support services.
For more information on how West’s service and solutions can help define, de-risk, and execute a product strategy from component selection to combination product release testing, visit the Integrated Solutions Platform page or contact a member from the TCS team or an account manager.
FluroTec® is a registered trademark of West Pharmaceutical Services, Inc., in the United States and other jurisdictions.
Crystal Zenith® is a trademark of Daikyo Seiko, Ltd.
FluroTec® and Crystal Zenith® technologies are licensed from Daikyo Seiko, Ltd