Elastomer Fundamentals: What Makes a Rubber Formulation?
The first thought that you may have when you hear the word “rubber” is natural rubber – a poly-isoprene-based polymer, which has as its origination the latex fluid drawn from rubber trees (most prominently in Indonesia and Malaysia). Although natural rubber has been used in the past for pharmaceutical applications, potential issues with latex allergies resultant from proteins from the original latex, have led to the almost complete adoption of synthetic rubber.
![]()
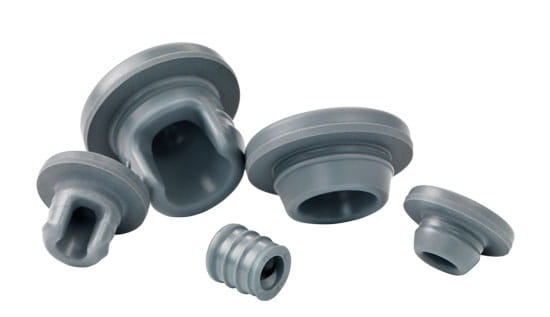
One of the main synthetic rubber types currently used for pharmaceutical applications is halobutyl (CIIR: chlorobutyl rubber, and BIIR: bromobutyl rubber) – developed in the 1950s and 1960s. The monomers comprising halobutyl rubbers are based on isobutylene (~98%) and isoprene (~2%) – both derived from oil. Halobutyl rubbers combine low gas permeability, good durability on exposure to moisture and heat, and good chemical stability. This makes them an ideal match for pharmaceutical closures, such as stoppers or plungers. The halobutyl rubber is, however, just one component of a complete rubber formulation.
The base rubber comprises the major amount, of course; in addition there are for instance fillers, pigments, curing agents, accelerators, activators and plasticizers. A formulation is designed very carefully to give the right properties (e.g., hardness, color, extractables and leachables profile) – in order to give the right performance. Over time, numerous formulations have been developed by West and optimized for maximum functional and chemical performance – especially in regard to extractables and leachables profiles.
Technical Customer Support (TCS) helps customers not only in choosing the optimal rubber formulation, but also with extractables and leachables information. For more, contact a TCS representative, or visit the West Knowledge Center.